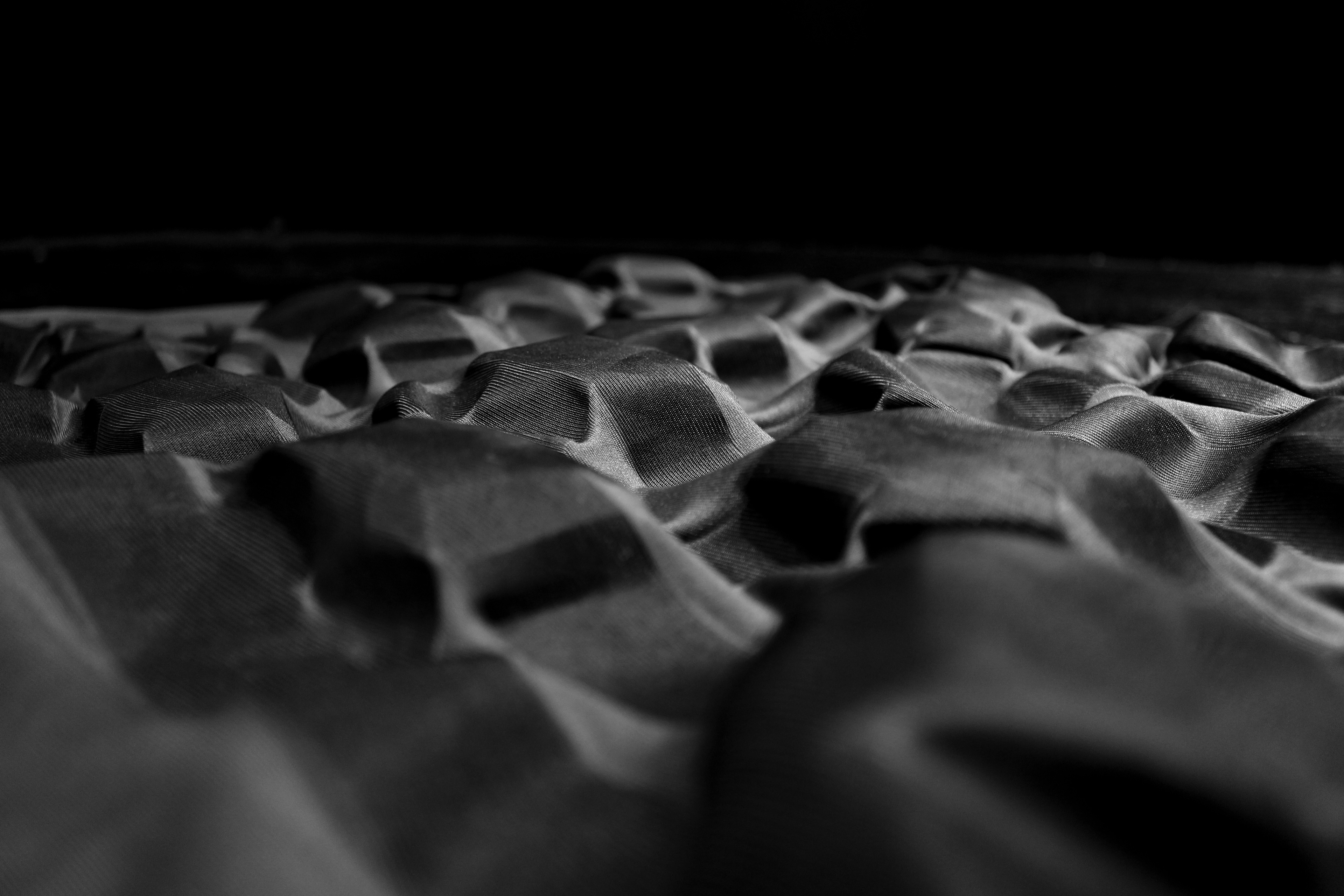
In order to activate the rigidizing properties of thermoplastics, heat and pressure must be applied. The proper amount of these two forces will slump and melt the fibers of a composite knit together into a solid structure. As a poor conductor of heat, the plastics will cool rapidly, allowing the fabric to maintain its given shape. Once released from tension, the heat-treated areas attempted to remain rigid as the unheated areas contracted to their rest state. This produced a deep surface topology.
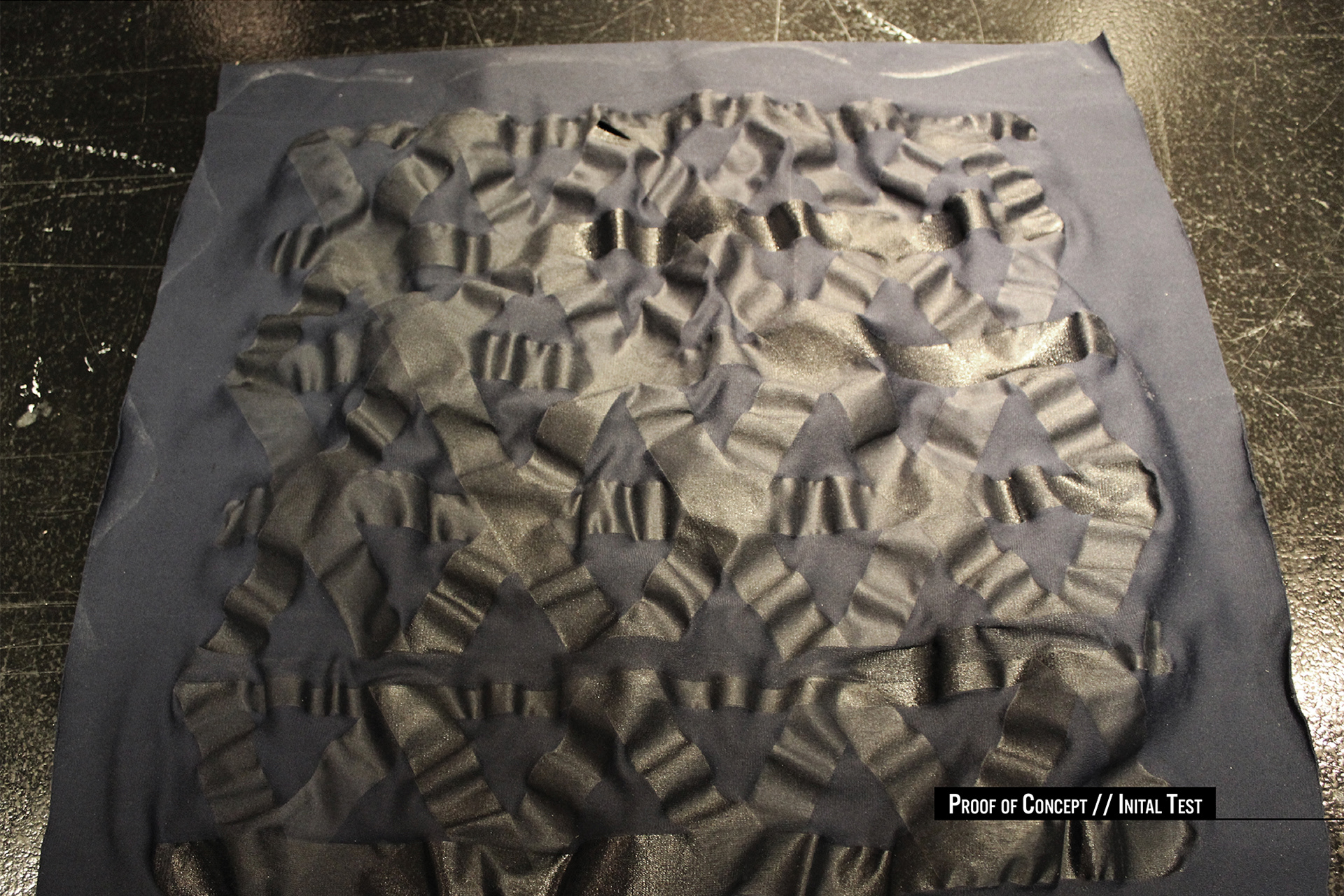
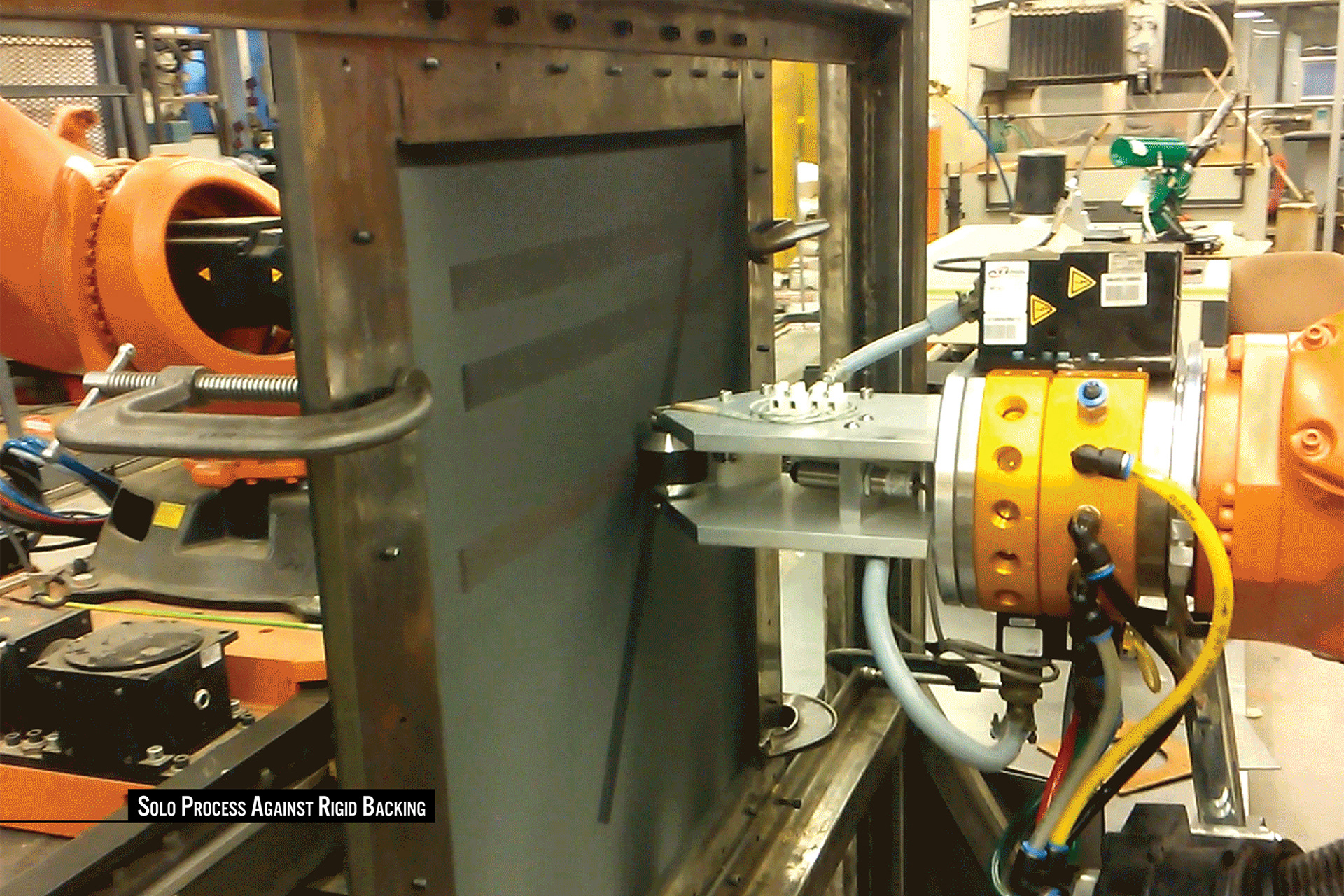
The second series of tests utilized a hybrid-stretch cordura, a technical fabric used in the outdoor garment industry. its 85/15 nylon/spandex composition was similar to the first test, but the weight of the fabric was several times greater. Theoretically, this would provide more material to help rigidize the fabric once released. In the final series of tests, two robots were used to provide pressure instead of a backer board. This proved to be much more sensitive to issues of fabric tension.
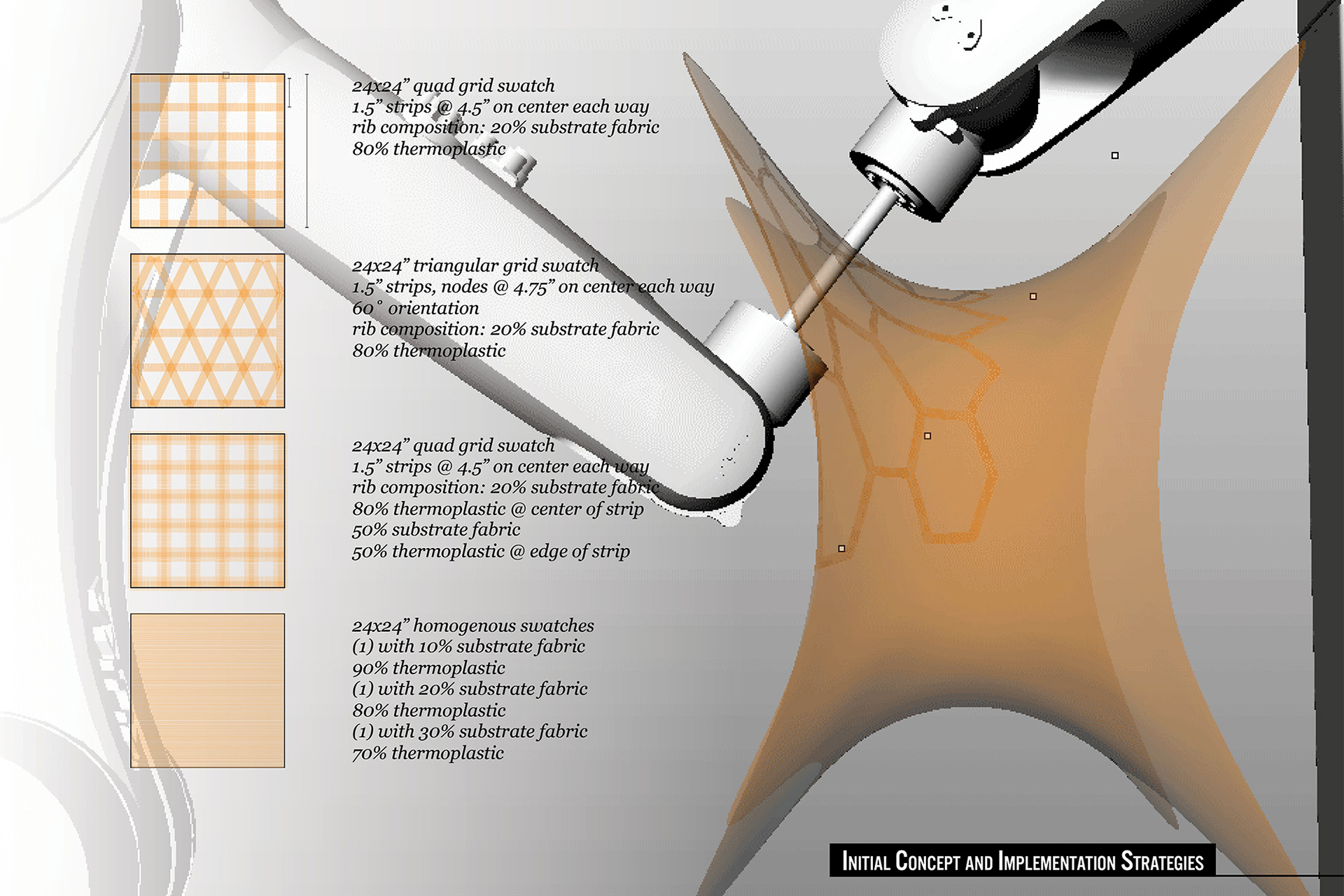
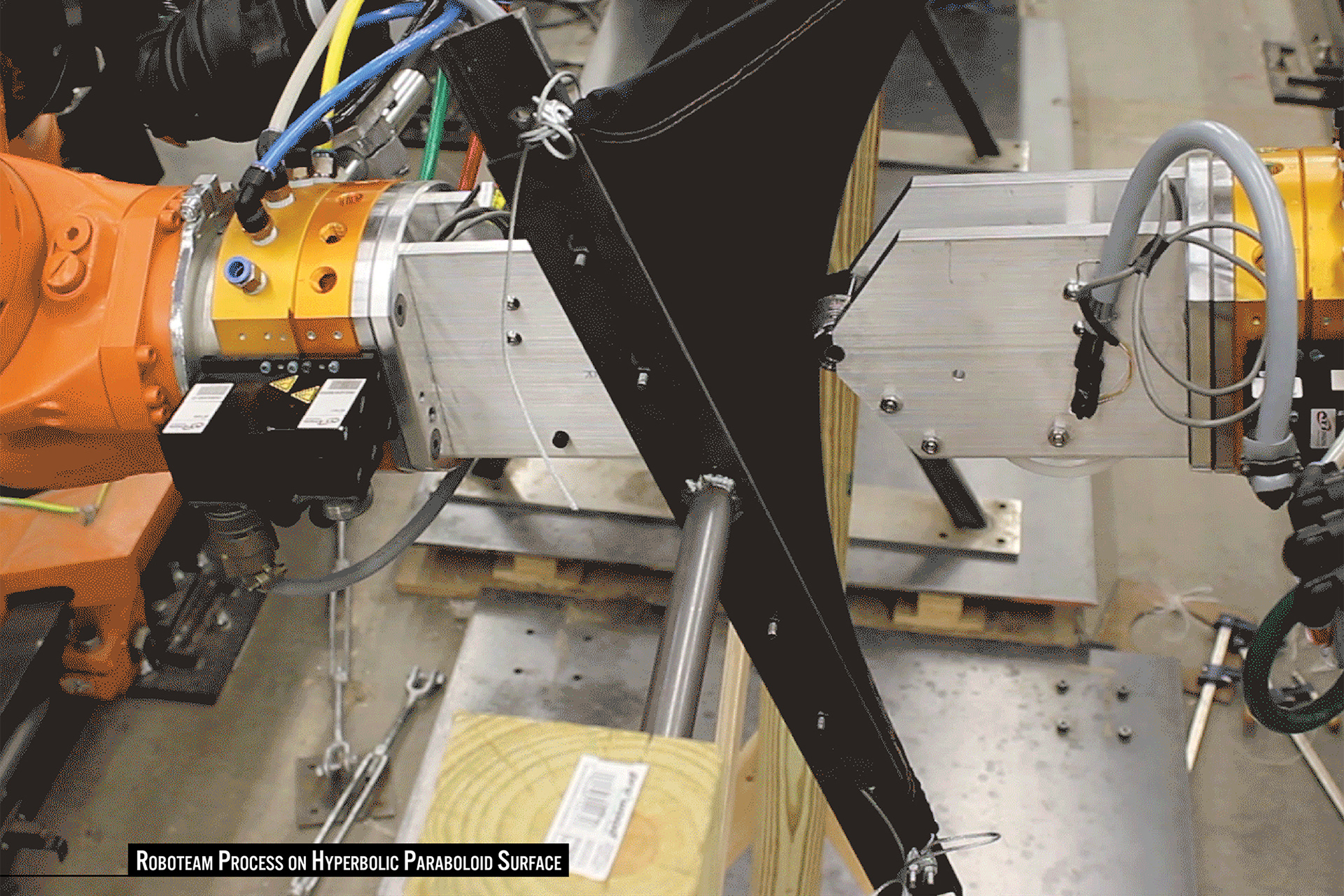
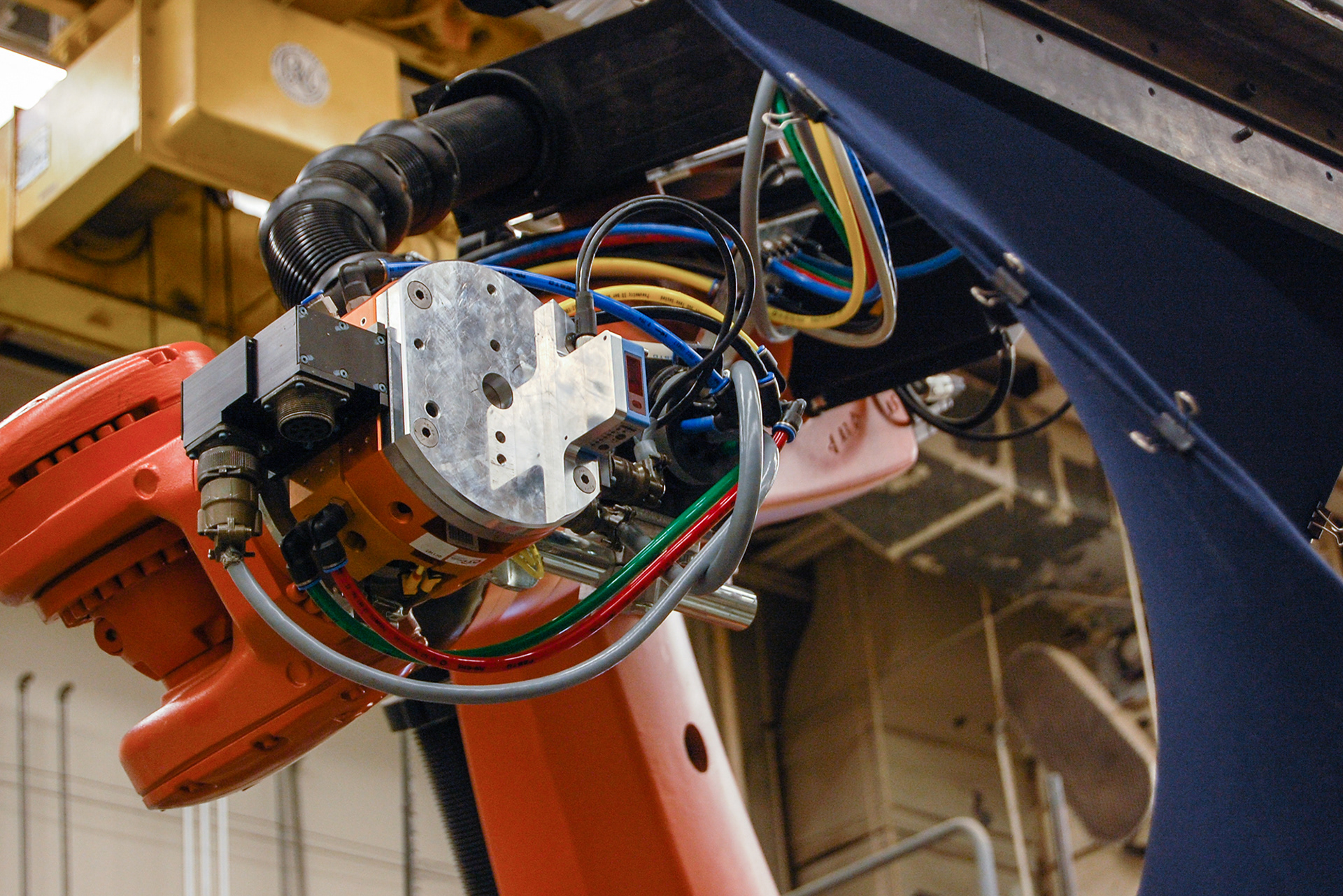
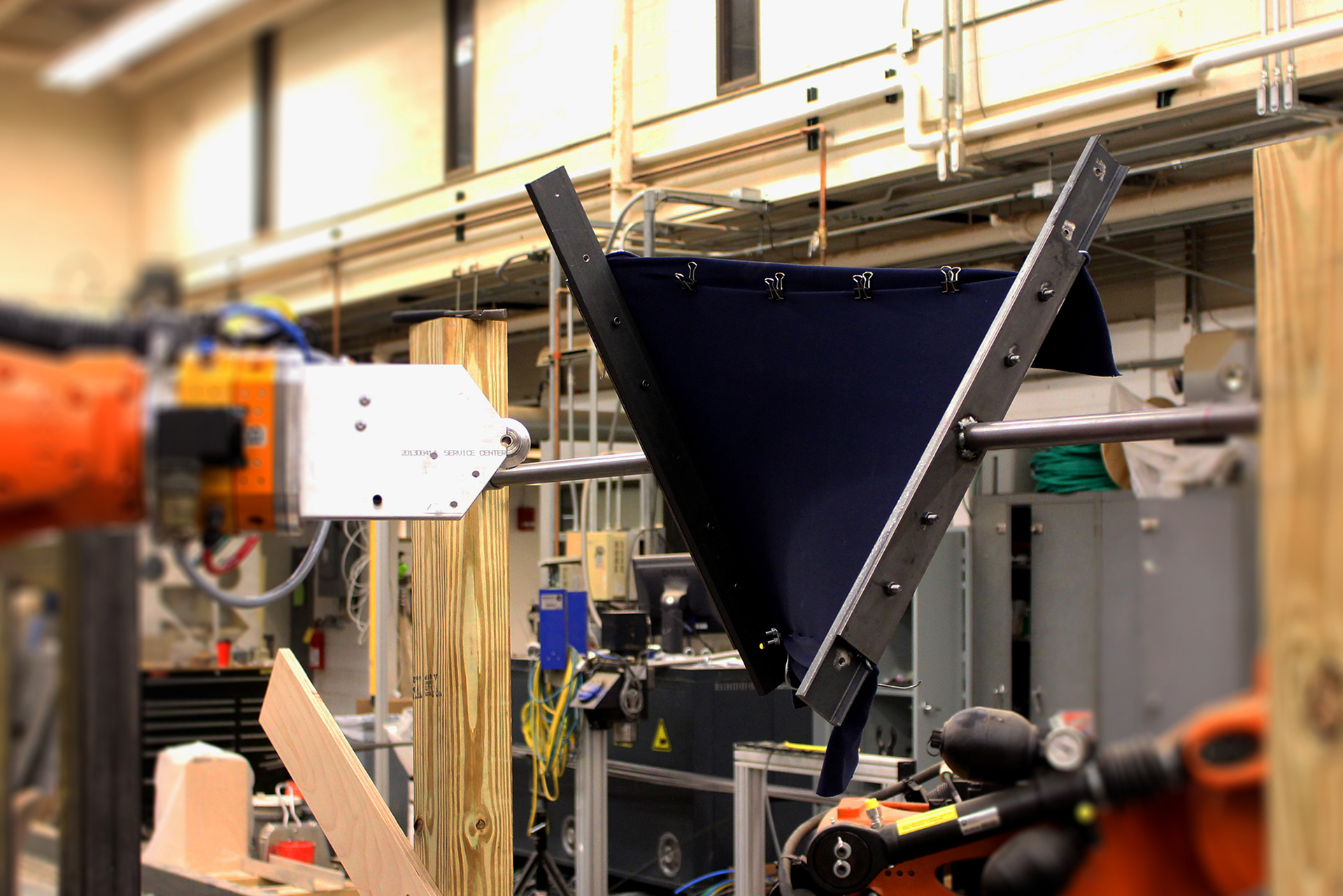
The tool developed by this project in conjunction with the carbon fibre lamination research trajectory continued to be used and iterated upon by the Taubman FabLab.
Digitastic Thermobots was a research project by Peter Shaw and Luis Orozco, in conjunction with Tutors Sean Alquist and Wes McGee's 2015 Research Through Making Project "Knit Architectures".
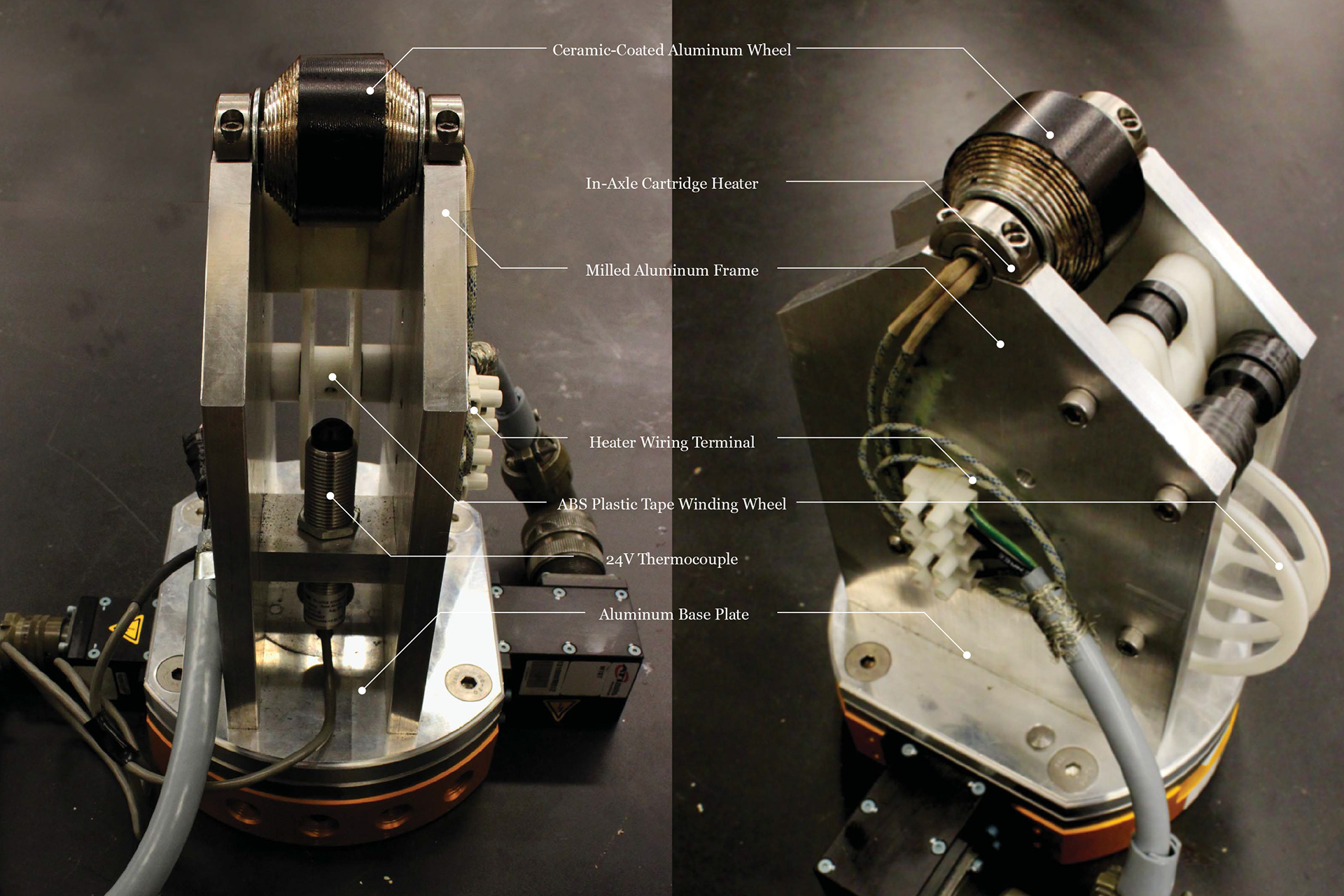
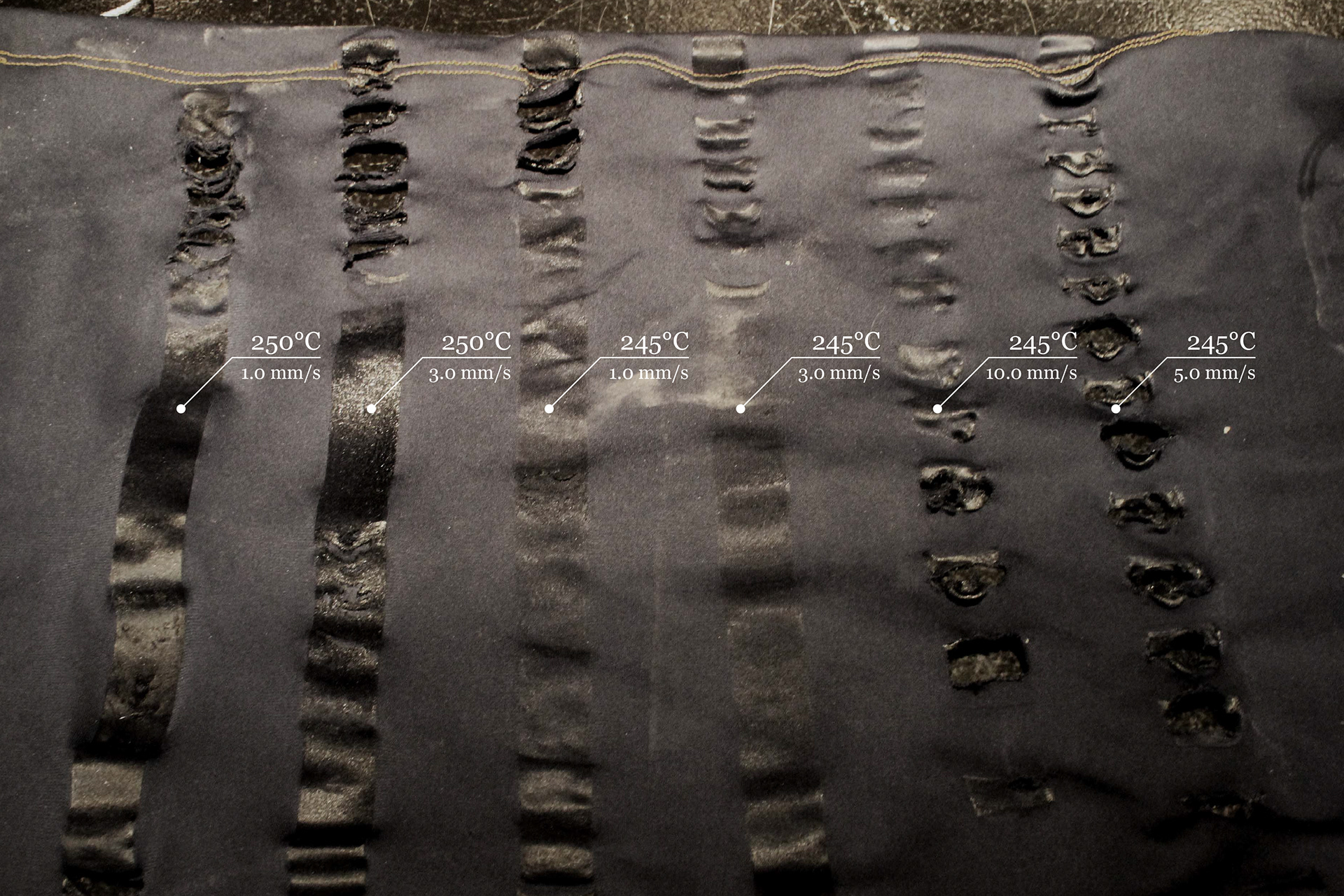